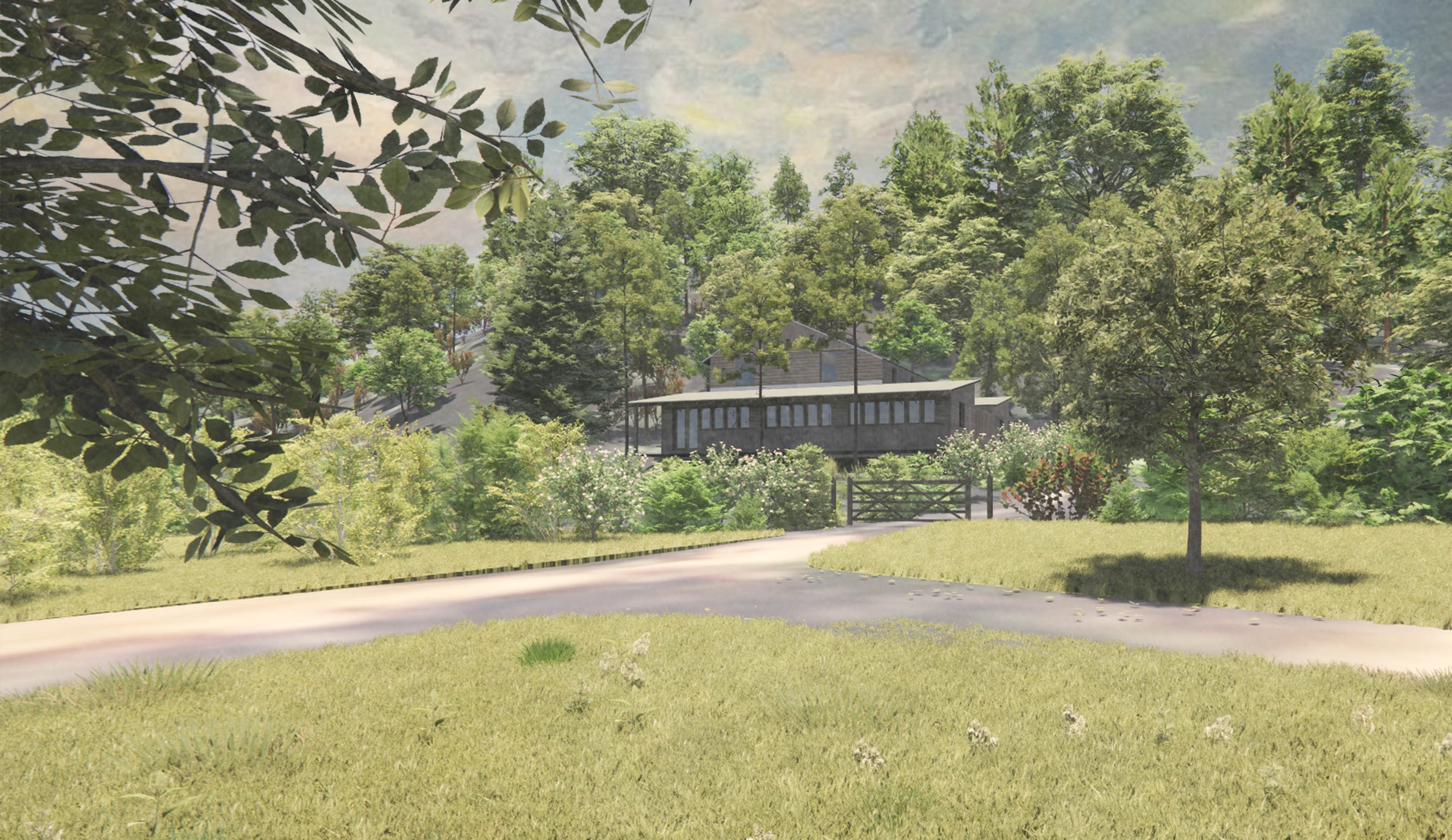
Bickleigh Barn Passivhaus, Tiverton
Built into a steeply sloping woodland site, the existing workshop has been thoughtfully designed to be converted into an exemplary low carbon, energy efficient family home that fits harmoniously within its surroundings. Leaning into the site’s agricultural barn context, the design draws inspiration from local materials, utilising site-sourced, home-grown timber cladding from Bickleigh Sawmill and durable corrugated metal roofing to enhance the aesthetic and environmental credentials.
This thoughtfully crafted detached building incorporates a well-planned home office, an inviting exercise area, a functional plant room, and a spacious multi-functional family room that caters to various activities. The clients expressed a desire for a building that not only connects seamlessly with the beautiful rural landscape but also reflects their deep appreciation for the natural woodland site. Another primary aim of the project was to create an exemplary low energy home that meets Passivhaus levels of performance, demonstrating a commitment to sustainability and comfort.
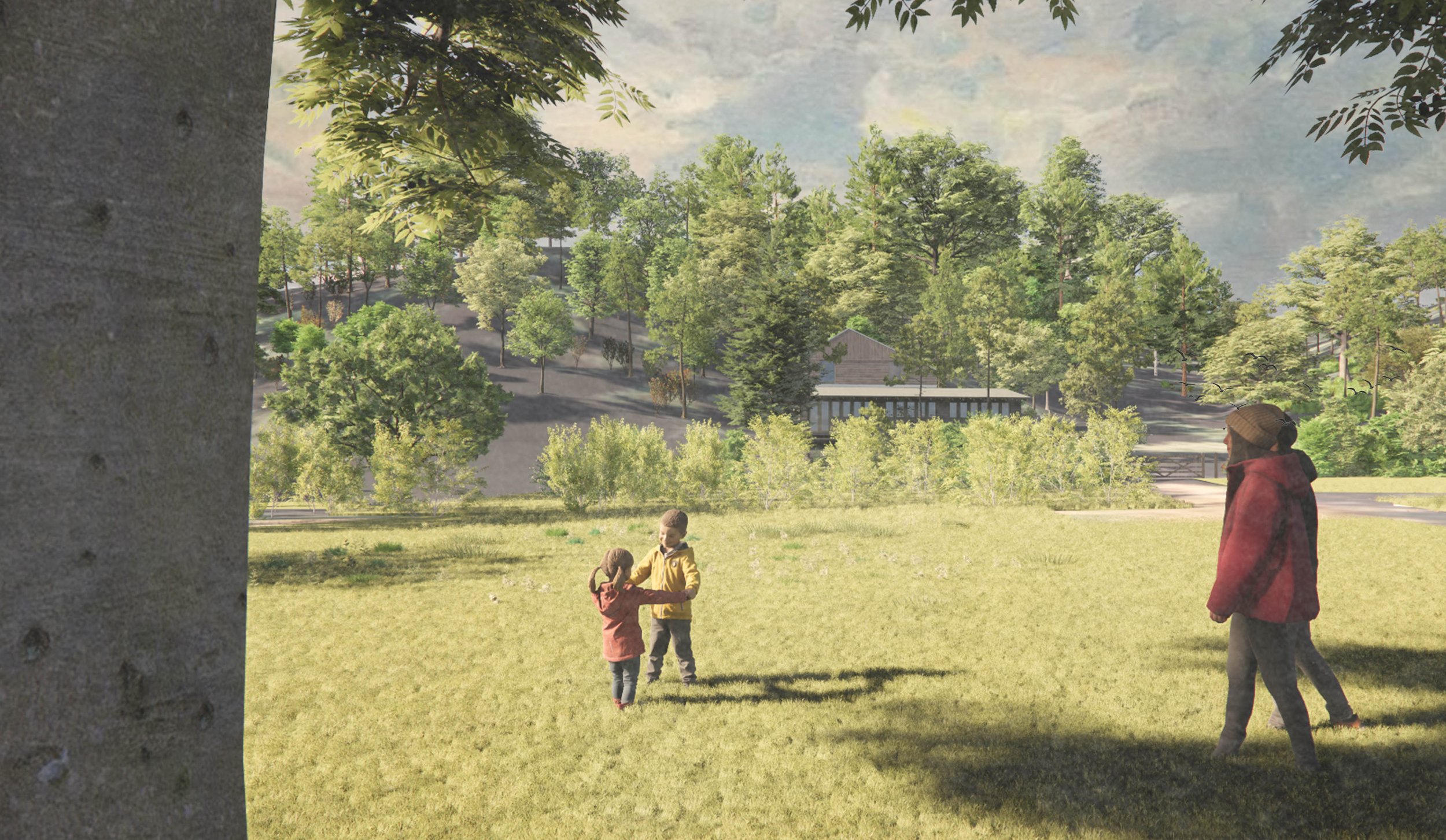
In terms of the external design, the proposal seeks to reflect that of a modern yet rural dwelling to maintain this appearance and setting in the countryside. The existing material palette has informed the proposed timber cladding to match existing. The agricultural/industrial corrugated roof is being replaced with a ‘wrinkly tin’ corrugated metal to reflect the agricultural context. The fenestration will comprise of powder coated aluminium frames with galvanized steel rainwater goods. The subtle and muted palette of materials allows the building to continue to blend into the background woodland.
The vertical nature of the site (with exposed tree trunks) and the existing buildings vertical window fenestration have been followed with the proposed vertical cladding and window fenestration.
The window openings elsewhere reflect a clear opening without mullion/transom to reflect the openings found in both vernacular and contemporary agricultural buildings and also learns from the existing window detailing.
Embodied Carbon:
In the context of national targets to reach zero carbon by 2050, and Devon’s earlier target of 2030, we must consider the carbon impact of architectural designs, and the materials we specify. By converting the existing workshop, we are ensuring the carbon that has already been ‘locked-up’ in the building, remains so. By sourcing materials from local manufacturers, we can reduce the emissions associated with transporting materials vast distances, often oversees. The timber used on this conversion can be directly sourced from Tasters Wood near to the site, not only dramatically reducing the carbon associated with transporting materials, but also ensuring the building is truly ‘of its site’.
Renewables:
The proposal seeks to use mechanical ventilation throughout using a Mechanical Heat Recovery unit (MVHR). This is highly efficient ventilation system which improves internal air quality and energy efficiency by transferring heat from stale air to fresh air. A combination of solar PV and air source heat pump (ASHP) will be used for heating and hot water.
The approach to the massing of the proposal has been thoughtfully considered given it’s context. The scale and massing follows the footprint of the existing workshop. The principle eastern façade is retained in its form and scale. To enable light into the deepest part of the plan, a small portion of roof is removed, which in-turn breaks down the massing to the northern entrance elevation. The height of the single storey north-western bay which forms the garage/store is reduced.
Sustainability is a key driver for the project. We believe passionately that in order to create a home that is fit for purpose and future proofed in the context of our national drive for a zero carbon society, we need to consider how we minimise the environmental footprint of our homes and deliver a low carbon development.
Passivhaus Enerphit:
Our primary focus is in reducing the building’s energy demand. The biggest energy consumption in housing is heating, so by increasing the thermal performance of the building fabric and building to a rigorous performance standard such as Passivhaus, we can reduce the demand for energy and consequently the number of renewables needed to offset demand. By taking this fabric-first approach, we can also ensure that the energy costs associated with the operation of the building are significantly reduced.
Energy modelling:
The proposal has been designed to meet the exemplary Passivhaus Enerphit standard. When modelled in PHPP the calculations show the space heating energy demand reduces to just 17 kWh/(m2a), which represents an 86% improvement when compared to the already approved planning permission for the converted workshop.
One of the key design moves we have made is to ensure all the living spaces are orientated south. This allows us to maximise solar gains and natural light. Heat losses are also minimised by vastly reducing North facing openings. We propose to convert the workshop by insulating above the existing concrete floor. The existing timber frame walls, and roof to the east are to be retained, and insulated. To meet Enerphit standard the depth of the walls and roof need to be increased to limit the heat losses. The first-floor element to the southwest will have the same insulated timber frame to the walls and roof. The existing timber frame windows are single glazed, the proposal replaces these with triple glazed timber/aluminium composite to dramatically reduce heat loss.